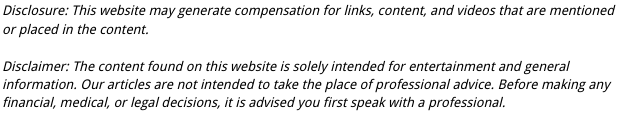
Good manufacturing practice is a system put in place to oversee that any products manufactured meet the set standards. These standards come in handy in minimizing the risks involved in any pharmaceutical production. Ideally, GMP synthesis regulations takes care of all aspects of the pharmaceutical output, from storage to hygiene levels of the members of staff.
GMP compliance not only improves a company’s reputation but also goes a long way in protecting the consumer from harmful product. It also protects our environment. Below are some basic GMP guidelines that every pharmaceutical company must adhere
to.
1. Quality Management
The main goal of quality management is ensuring that the product manufactured is good enough for its intended use and does not expose the consumers or the environment to any risk. Quality management is achieved by implementing other aspects, such as quality assurance, quality control, and quality risk management.
2. Sanitation and Hygiene
No pharmaceutical manufacturing process can meet the set standards with mediocre hygiene standards. The sanitation and hygiene guidelines comprehensively cover anything that can lead to contamination of the final product. That includes members of staff, equipment used, as well as any other production material.
One fundamental way to prevent contamination is by identifying a potential source, then getting rid of it through an efficient hygiene program.
3. Structures and Manufacturing Premises
The environment in which your production facilities are situated matters a lot. You must ensure that it is free from any potential risks of contamination. Also, the premises’ design should be in such a way that maintenance and cleaning are easy.
4. Equipment
Manufacturing equipment needs maintenance from time to time. Maintenance involves proper cleaning as well as fixing any faults to avoid errors while manufacturing pharmaceutical products. Any equipment such that is not functioning correctly should be labeled as faulty to prevent losses that could be as a result of producing substandard products .
5. Raw Materials
Pharmaceutical products need various raw materials. GMP storage conditions dictate that the raw materials should be stored properly, as the manufacturer has specified. Proper stock keeping is also another critical factor in ensuring compliance with the GMP synthesis Guidelines. The raw materials you use should be accurate and of high quality to subsequently produce a high-quality product.
6. Personnel
No matter how much you invest in any other GMP synthesis compliance guidelines, success heavily relies on the staff. Always ensure that you hire qualified people for the job. If the wrong person lands the job, the risk of producing substandard products are higher despite everything else being right.
All workers in a pharmaceutical production plant should be conversant with all GMP quality control guidelines. There should also be stringent rules on hygiene that all workers should follow. The managers should be clear in allocating duties to prevent conflicts at work, which can affect production.
7. Handling Complaints
Although it might sound minor, listening to complaints could be the best way to identify any loopholes with your production. Every pharmaceutical company should have a functional GMP complaint system. Besides receiving complaints, the company should ensure that they come up with a realistic solution to the problem.
8. Proper Documentation and Recordkeeping
Adequate documentation is core when it comes to GMP quality assurance. Accurate records make it easy to track the history of a company, even in the case of a change in management. The files also contain crucial information, such as the expiry dates of various raw materials.
In case there is a hitch in the production process, the cause of the problem can be identified by checking through the record. These records should be reviewed from time to time for accountability.
9. Inspections
Officers should inspect the pharmaceutical production process to ensure that all the guidelines are met. The officers should then recommend any steps that would be taken to improve the production process.
10. Sustaining GMP Synthesis Compliance
All the GMP regulations are set to ensure that pharmaceutical products are safe for human consumption. Therefore, companies should strive to maintain compliance. One of the best ways is conducting surprise audits.
If you audit your company on notice, chances are, you won’t get accurate results. On the other hand, surprise visits will give you a real picture of what happens. The members of staff will also feel obliged to follow all the rules always.